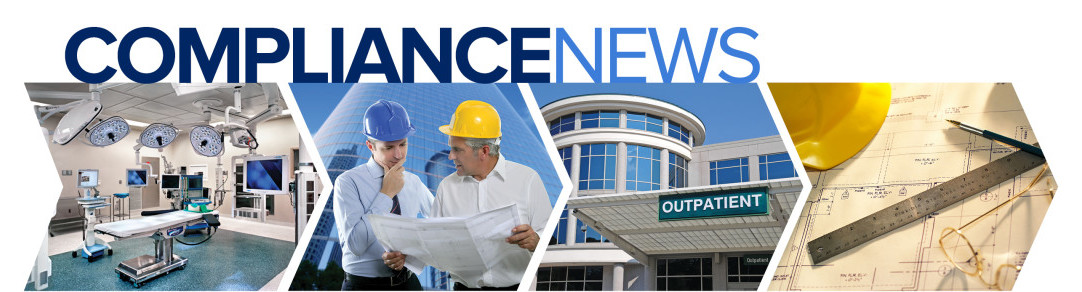
Compliance News: Predictive Maintenance and Condition-Based Maintenance
Predictive Maintenance (PdM) or Condition-Based Maintenance (CBM) can help facility professionals solve problems they don’t even know about yet.
Many health care facilities currently have ongoing Preventive Maintenance (PM) programs that consist of lists of activities to be performed at calendar-based intervals. Sometimes those PMs are based upon past practices, and sometimes they are based upon the original equipment manufacturer (OEM) recommendations. CMS Tag A-0724 requires that the surveyed organizations be able to prove compliance with the following hierarchy of requirements:
1.Law and regulation (always)
2.Manufacturer recommendations – if there is no CMS-compliant Alternative Equipment Maintenance (AEM) program in effect
3.Alternative Equipment Maintenance (AEM) Program requirements
Oftentimes organizations believe their PM programs are compliant with OEM recommendations but they are not able to prove that compliance because of the absence of documented proof during survey. Regardless, there is an option provided that the organization has a CMS-compliant AEM Program.
Predictive Maintenance (PdM) is also sometimes called Condition-Based Maintenance (CBM). There are more similarities than differences, and many people now use those two terms interchangeably. This article will use PdM for consistency. PdM is an option mainly for organizations with a CMS-compliant AEM program unless the OEM recommends PdM.
The PdM equipment should consist of permanently installed and monitored devices where possible, supplemented by in-person PdM inspection and testing of equipment that does not contain those permanent devices. In both cases, maintenance should be based on the actual condition (health) of equipment obtained from in-place non-invasive PdM measurements, and/or manually performed non-invasive PdM inspections and tests. The ultimate goal in both cases is to identify proactive maintenance actions to be performed when the maintenance activity downtime is most cost effective, and with corrective activities completed before the equipment fails in service.
PdM can assist with reducing unplanned equipment downtime, minimizing time and cost of repairs and maintenance, ensuring equipment is available and in working condition, prolonging equipment life expectancy, and minimizing spare parts costs.
PdM programs often require effective Computerized Maintenance Management System (CMMS) and multiple Internet of Things (IoT) enabled devices. An increasing number of organizations are also using machine-learning technology for this purpose.
Examples of commonly-employed in-person PdM inspection and testing of activities are infrared scanning of equipment components and connections, oil samples drawn for follow-up testing from liquid-filled equipment such as medium voltage transformers, use of ultrasound technology.
A future article will discuss real-time acoustic and ultrasonic monitoring for detecting air-borne or structure-borne sound waves associated with Partial Discharge, pressurized systems leaks, and mechanical defects of rotating machinery.
Contact the author for more information, dstymiest@ssr-inc.com.