A Crash Course in 3D Scanning
Technology continues to impact how we live, work, and perform our jobs. Over the years, sustained advancements in technologies have dramatically increased efficiency and productivity in our daily lives. In the AEC industry specifically, these developments have resulted in additional demands on building projects by increasing the pressure to expedite and accelerate project timelines. One of the best tools on the market right now to accomplish this is the use of 3D scanning.
What is 3D scanning?
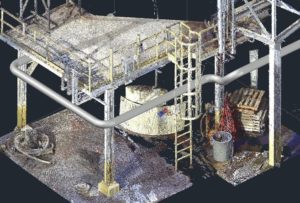
Proposed piping route is modeled in the 3D point cloud to find conflicts.
3D scanning is an affordable and efficient way to thoroughly document, record, and measure a facility or building site. It uses LIDAR and photogrammetry technology to collect data and produce a detailed 3D interactive model of your project area. It is a labor-saving way to collect precise 3D measurements of physical objects, producing accurate results even in complex environments such as a crowded industrial plant. The data is then collected and compiled into a 3D point cloud. This 3D point cloud can be exported and used in tandem with today’s most common design programs like Revit, AutoCAD, and MicroStation. The end result is a digital file that allows the user to have access to an incredibly detailed 3D version of their project or facility. This enables the owner or design team to take accurate measurements, render to scale models in existing facilities, and identify design conflicts without even stepping foot on site.
What value can 3D scanning bring to your project?
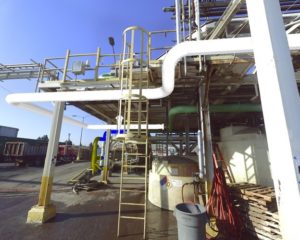
Proposed piping route is overlaid inside the interactive 3D model to identify conflicts.
The largest advantage to using 3D scanning is the positive impact it can have on your design timeline. By providing accurate measurements, accessed from anywhere, the design team can model and design the proposed project elements with precision. It eliminates the unknowns that are typically hard to identify with only field measurements or due to a lack of existing drawings. This allows the design team to produce better design documents.
These scans are particularly advantageous for renovation or addition projects. One of its best uses is to identify design conflicts. By using the 3D point cloud to model the proposed structure, piping, or equipment in real space it is easy to visually identify potential conflicts that are easy to miss during the coordination phase. This reduces the extra time that is typically spent during construction addressing conflicts. The reduction in time spent dealing with these issues can have a huge impact on your project timeline. In addition to this, when a construction issue does arise, the design engineer can immediately begin working on a solution. A site visit is not necessarily required since the design team has access to a digital 3D version of the facility.
What can you expect if using 3D scanning on your project?
A full 3D scan costs on average between $4,000-$12,000 depending on the project size and complexity. To start the scan, an individual data collector will spend one to two days on site in order to acquire sufficient data points. The collection process is not disruptive to a facility or their daily processes. After collection, the scanning company will begin to compile the individual data points from the site. After one to two weeks, a full engineering package is completed and delivered to the owner. This package allows the owner and design team access to an interactive 3D model that allows the designer to model and measure the proposed project area in real space as it is. The outputs can be delivered as pictures, 3D interactive models, point clouds, and even full Revit models.
Conclusion of Benefits
In today’s fast-paced and challenging construction environment, the AEC industry has been forced to take a hard look at project workflows. Taking advantage of new technologies, like 3D scanning, brings value to each phase of a project. For a relatively small investment, owners can utilize 3D scanning on projects to streamline the design and construction phase, saving time and money throughout its duration. The benefits that this technology adds to a project result in a better and more cohesive product for all parties involved.
- Reduced design time
- More accurate design documents
- Reduced RFIs as unknowns are identified on the front end
- Reduced construction time since conflicts are more easily avoided
- Reduced consultant travel time and costs
- Accurate record keeping