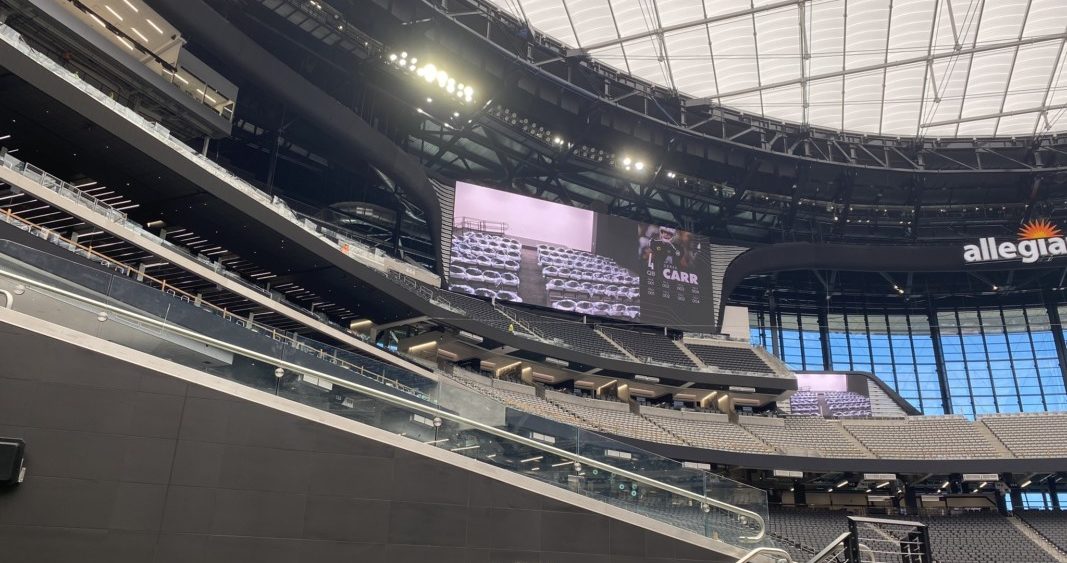
Evaluating Fabric vs Sheetmetal Ductwork
Iconic but future-proof, innovative with a community-focus. These are some of the expectations of new sports and entertainment venues being built around the world. Ownership teams are looking for jaw-dropping designs that appeal to fans, deliver a competitive advantage to the home team, and often anchor a massive entertainment district intended to revitalize a community. In response, architects are delivering intricate designs that create multifaceted challenges for engineers. The days of simple HVAC design to maintain comfort for players, teams, and fans in an arena or stadium are long gone. The complex geometries of the buildings and the required structural elements supporting these massive structures have created a new set of challenges for the design team. SSR has stepped up to meet these new challenges. The design team must now consider the location of air delivery and ability to direct airflow within the bowl while balancing the ability to properly control the indoor environment. As an engineer, the seating bowl HVAC system is the foundation to delivering a memorable fan experience while at the arena. In order to achieve success, there are four key areas that should be evaluated: fan experience, acoustics, flexibility, aesthetic, and overall cost.
One of the most important elements in venue design is planning for the fan experience. Temperature and humidity, which impact physical comfort, make a lasting impression long after the final horn has sounded. The ability to maintain temperature and ensure comfortable conditions for 20,000 people during a single event is no small task, and proper bowl air distribution and ductwork design is required. Conventional design has centered around large, double-wall sheetmetal ductwork with sidewall grilles or jet throw, drum diffusers aimed at the various spectator sections throughout the seating bowl. While this design has worked for numerous years, the limited number of grilles handicapped the system, creating hot and cold zones within the venue. In addition, as grilles and diffusers age, they often start to drift and become unbalanced, which then creates uneven airflow. In recent years, the ability to provide a more consistent and continuous airflow across the seating bowl has been achieved with the implementation of fabric ductwork systems. This design, which can be tested and verified through computational fluid dynamic (CFD) models, paves the way for the future of arena bowl design.
In addition to thermal comfort contributing to fan experience, the acoustics of the bowl play a key role as well. The arena bowl is a unique acoustic space that must provide for quality sound across a variety of events with different seating arrangements. An arena can host the symphony one night, a rock concert the next, and a hockey game the following afternoon, each event requiring different acoustical performance from the facility. Ductwork located in the superstructure of the facility plays a key part in acoustics of bowl design. Conventional sheetmetal ductwork increases noise generation due to radiated noise from sidewall grilles distributing air to the space. The use of fabric ductwork reduces the overall airborne noise to the space by supplying air through engineered orifices to distribute air, which eliminates grilles, balancing dampers, and noise generated by these devices. The inherent design of the fabric provides a quieter air delivery due to the pre-engineered orifices, evenly spaced along the entire ductwork run to distribute the supply air to the space.
When evaluating sheetmetal verses fabric ductwork, one of the key differences is the aesthetic flexibility fabric systems provide. Fabric duct systems can be provided in a wide array of different shapes, sizes, and colors. This flexibility allows the design team to rethink the traditional norms surrounding bowl ductwork design and provides the architect another resource to help achieve their artistic vision. Conventional metal duct systems lack this level of flexibility and are therefore limited when it comes to design options. With a conventional system, the goal has always been to install it high into the structure to hide it as much as possible. Alternatively, the recently completed Allegiant Stadium (home to the Las Vegas Raiders) highlights the world’s largest oval fabric duct system by suspending it from the stadium roof structure and creating an architectural ribbon element along the entire upper seating bowl which provides a striking design and delivers a comfortable environment for Raiders fans.
Most of today’s venues are truly multi-purpose and could host up to 300 events in a single year. With limited time between events and limited operations staff to stage for the next, there is little time for ongoing maintenance such as cleaning ductwork and readjustment of supply air grilles. With a fabric system, the need for cleaning dust and debris is minimized. The fabric is porous and allows a very small portion of the air to escape through the fabric skin, providing just enough pressure to avoid dust collection, unlike a conventional system which has a constant build-up of dust. A fabric ductwork system also provides flexibility for facility operators to allow various sections of the system to be deactivated during a concert where the movement of air might hinder the theatrical performance including fog, smoke, or pyrotechnics. This provides the facility with full-scale flexibility based on the artists’ or events’ needs each night.
A big factor in the debate between conventional sheetmetal and fabric ductwork is construction cost. In today’s market, cost is a major driver of decisions. If all variables are held equal and the two systems are compared, fabric ductwork systems are somewhere between 30-50% more cost effective than a conventional sheetmetal double-wall system. A substantial amount of the cost savings is realized in labor required to install the system. Fabric systems come in modular sections; much like assembling a shelf, you begin with individual frame pieces, assembling them first, then you install the outer fabric around the frame to provide a complete system. This assembly is typically performed on-site in the bowl structure suspended above the event floor. This eliminates the need for multiple lifts which are often required for large sheetmetal ductwork when fully assembled. In addition, fabric systems weigh far less than sheetmetal ductwork. Lighter systems require less structure to support them; therefore, the resulting structural savings can be realized during construction or could be added to maximum rigging capacity of the venue roof structure.
While HVAC systems and supporting supply air ductwork systems might not be the most glamorous aspect of an arena or stadium — and doesn’t garner attention like state-of-the-art technology — they do have significant impact on fan and player experience, operational flexibility, and first costs. A properly designed ductwork system contributes to the overall success of these venues. We attend events and games for the experience, connection, and sense of community that surround such gatherings. At SSR, our experienced team of venue engineers and consultants recognize the purpose behind these venues and strives to deliver a design that creates memorable experiences to those in attendance.
Allegiant Stadium & The Worlds Largest Fabric Duct System
The original architectural design vision for the interior of the stadium bowl included decorative ribbon elements that ring and frame the upper seating areas. The original design intent was for an architectural element to be the ribbon and a separate, large round sheetmetal supply duct to be located and hidden behind the ribbon for supply air to the upper bowl.
After many design iterations, SSR and the design assist team ultimately proposed the use of a large oval fabric ductwork that could serve both purposes. One fabric duct element to function as both the ribbon and the supply air ductwork. This design change resulted in a cost savings of $6 million with no loss of design intent.
Ultimately, the design change was approved by the architectural team and ownership. The large over ductwork measures 132” high and 72” wide and is the largest fabric duct installed in the world.