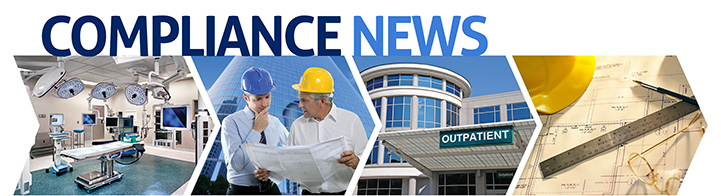
Compliance News: Best Practices for Reliable Power Systems
The March 2016 issue of Health Facilities Management Magazine discusses “Best practices for hospital power system reliability.” The following highlights some of the topics contained within that detailed article, and we recommend that Compliance News readers review and share the hyperlinked HFM Magazine article within their organizations.
Best practices can be undertaken throughout the life cycle of the power systems. The power system life cycle starts with planning, design, construction, installation and commissioning. It then continues with ongoing inspection, testing and maintenance. Existing power systems may have unknown vulnerabilities that can be uncovered and removed or mitigated. And finally management of the power systems should include identifying preferred failure responses and planning appropriately for them.
Recognizing that the following approaches may result in increased costs, some best practices related to design, installation and commissioning include:
- Minimizing physical risks due to environmental causes such as external flooding, internal flooding, wind-borne hazards, and other potential hazards
- Mitigating the impact of discrete equipment failures by incorporating mitigation measures such as power systems with multiple electrical utility feeds, main and tie device arrangements that can be switched automatically, manually or both, and means to connect portable equipment such as generator sets.
- Separation between normal power and emergency power equipment, including physical separation and fire separation
- Separation between similar systems (such as normal power “A” and normal power “B” for example) can also be considered a best practice to reduce the potential for “all eggs in one basket.”
- Requiring equipment details that facilitate ongoing inspection, testing and maintenance, such as infrared viewports, bypass-isolation transfer switches, and special maintenance features within electrical power switchgear
- Requiring full commissioning whenever power system components are installed or modified
Operations-related best practices may include the following:
- Creating and supporting current documentation of the information necessary responding effectively to internal power system failures
- Proactively determining the changing load on major power equipment as the facility evolves, including approaches such as power monitoring systems, portable metering and load profile analyses
- Regularly inspecting all high-value electrical equipment to find potential environmental and equipment problems before equipment failures occur
- Annual thermographic (infrared) scanning of electrical power equipment
- Testing and maintaining electrical power equipment maintenance in accordance with industry guidelines or manufacturer recommendations
- Educating clinicians about their electrical environments
Robust contingency planning for both internal and external power failures is a best practice, including:
- Validating that any existing power failure procedures will pass the responding staff member’s reality test before the failure occurs
- Realizing that most failures are partial internal failures rather than full utility failures, and planning accordingly
Finding unknown vulnerabilities and then mitigating their potential impact is a best practice. Some of the ways this can be accomplished include:
- Assessing physical installations and equipment
- Assessing training and communications
- Assessing the adequacy of inspection, testing and maintenance protocols
- Assessing the electrical safety program against NFPA 70E
- Assessing the adequacy of contingency planning documents
- Finding and then assessing hidden potential common-mode failure points
- Conducting power failure risk assessments and hazard mitigation
- Conducting power system vulnerability analyses
- Conducting power system gap analyses
NFPA DISCLAIMER: Although the author is the 10-year Chairman of the NFPA Technical Committee on Emergency Power Supplies, which is responsible for NFPA 110 and 111, the views and opinions expressed in this article are purely those of the author and shall not be considered the official position of NFPA or any of its Technical Committees and shall not be considered to be, nor be relied upon as, a Formal Interpretation. Readers are encouraged to refer to the entire text of all referenced documents. NFPA members can obtain NFPA staff interpretations at www.nfpa.org.
Questions related to this article may be directed to the author, David Stymiest, PE, CHFM, CHSP, FASHE, at DStymiest@SSR-inc.com.